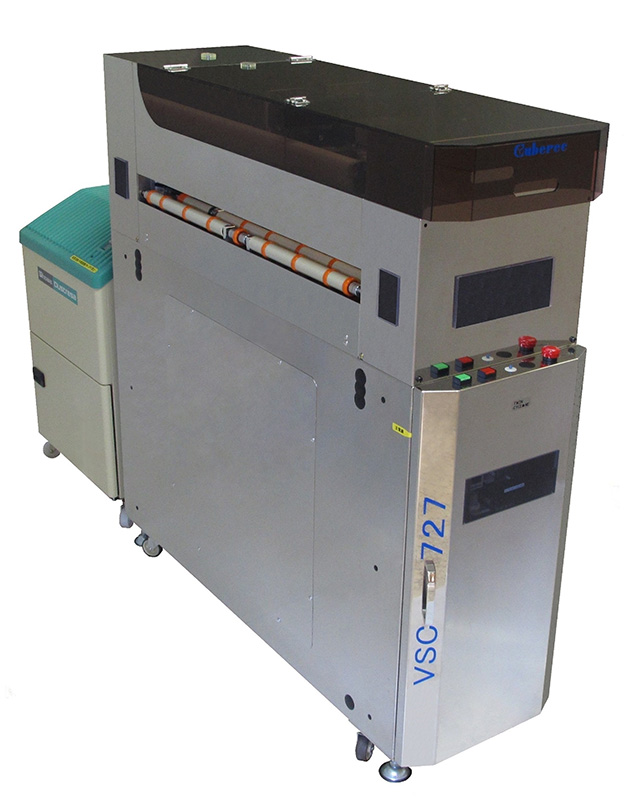
Enables adjustment of adsorption conveyor adsorption force
Adjust to optimum setting for board transport
A simple dry cleaner with just cyclone brush and dirt suction.
ECONOMY
ECOLOGY
EASY MAINTENANCE
Specification
Supported board width |
350~727mm |
Supported board thickness
|
Rigid board: 0.04~3.2mm |
Brush wire diam |
VSC:Approx 30µm
LSC:Approx 18~30µm |
Brush RPM |
1600rpm(60Hz) |
Dirt suction capacity |
5㎥/min 1.86kPa
Filter: Min.5µm, 99% collection |
Reference pass line |
895~945mm |
Conveyor speed |
0.6~3 or 1.8~6m/min |
Utility |
AC100~110V 9A incl. dust collector
Connectable CDA for ionizer |
Size |
W350×D1104×H1150mm |
Weight |
Main body:120㎏
Dust collector:50㎏ |
Twin cyclone principle
What is a twin cyclone?・・・
- Twin brush configuration : two brushes in series one above the other
- Top and bottom brushes both rotate inwards regardless of product flow direction, preventing contaminants from escaping outside.
- Contaminants swept to the inside of the brushes are efficiently sucked out through the dust collection hoses at top and bottom.。
- User-friendly design of cyclone head enables easy replacement of brush (cartridge type).
Ingenious, deceptively simple design
You can click1to check details.
1Utility
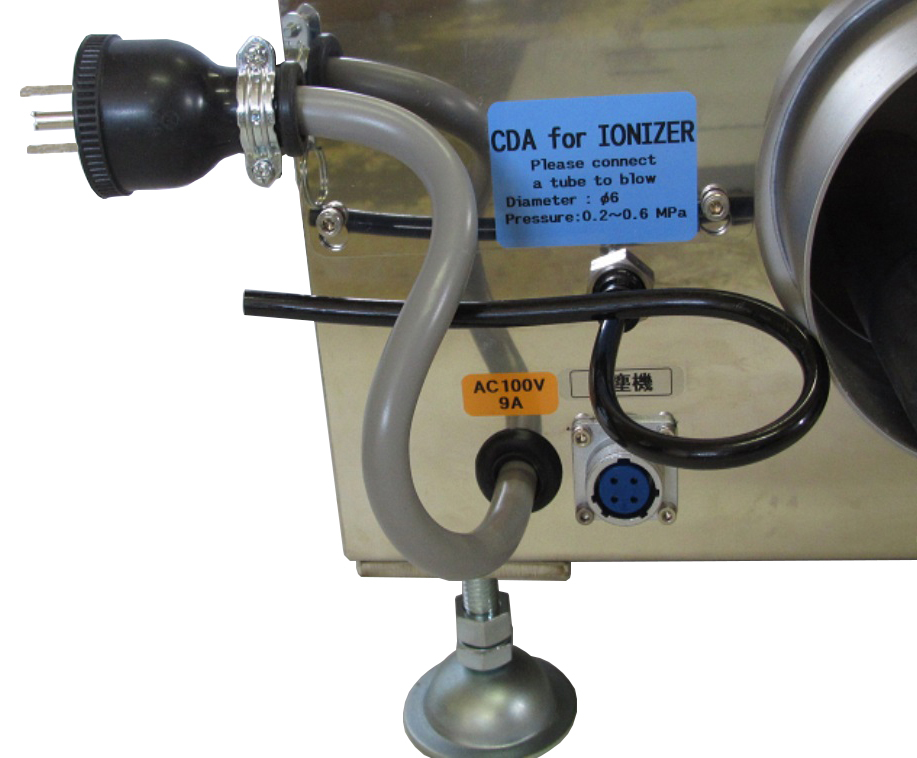
- AC100-110V 9A
- Connection of CDA (Φ6) to ensure efficient static electricity removal.
- Support for a variety of voltages.
※Manufacturer option
2Dust collector exhaust vent
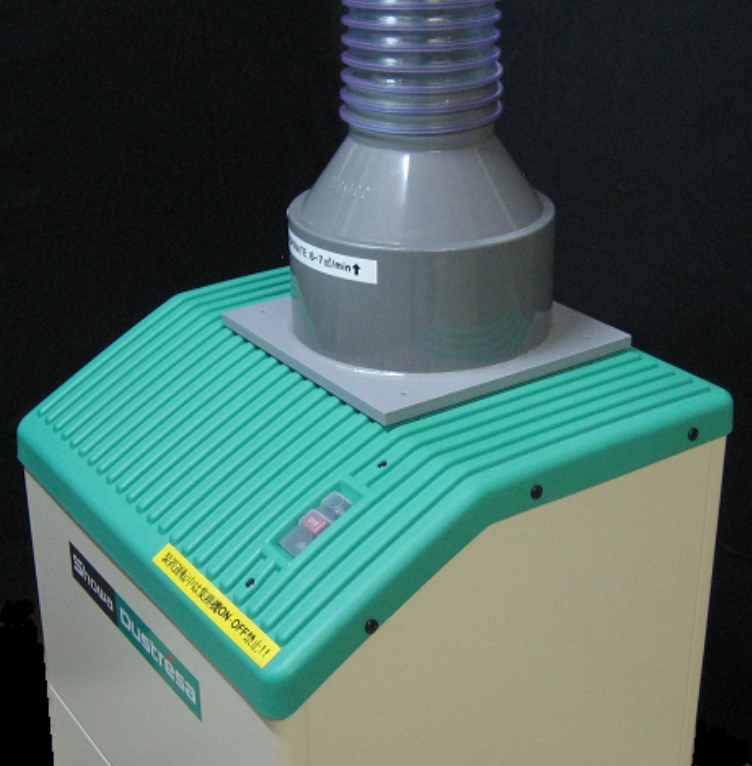
※Manufacturer option
- Support for connection to plant exhaust piping
- Essential for use in clean rooms
- Prepare duct of ID 125/150/200mm
3Adsorption conveyor damper

Enables adjustment of adsorption conveyor adsorption force
Adjust to optimum setting for board transport.
4Ionizers
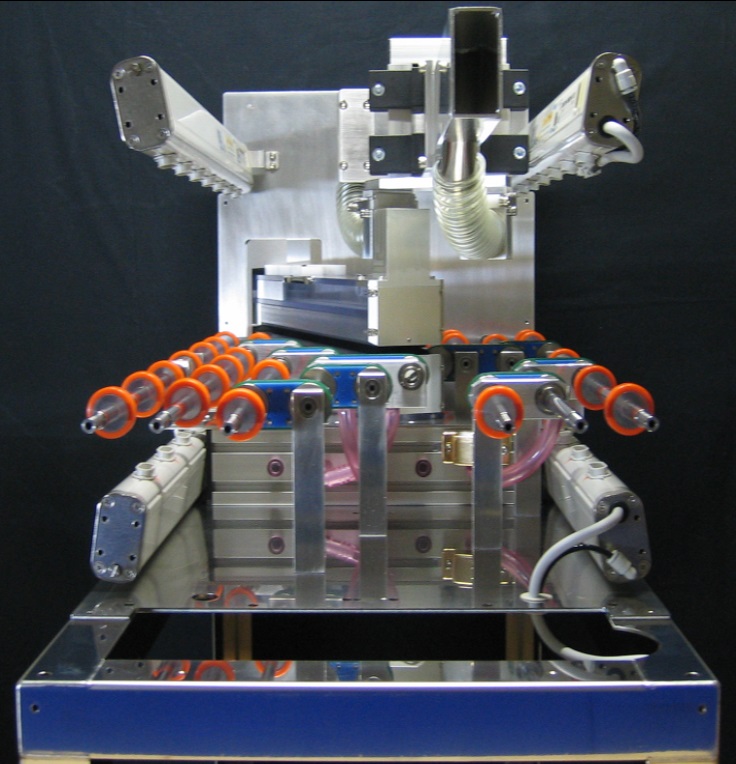
Fitted as standard at top on exhaust side
Can be fitted at up to 4 positions
※Manufacturer option
5Cyclone soft brush
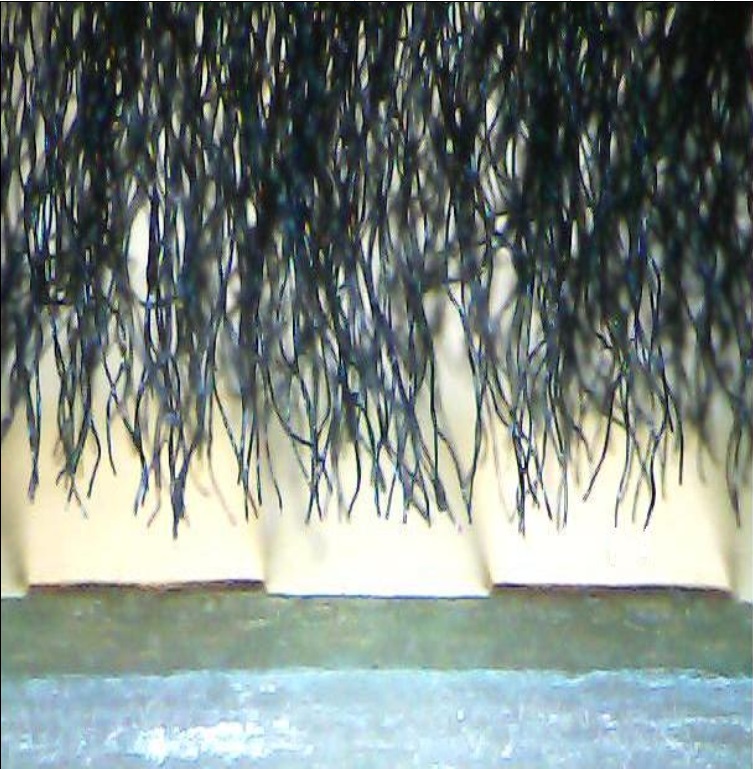
[For VSC]
Comprehensive support for dust filter, deburring, etc.
[For LSC]
Effective at scraping out at up to L/S75µm
Original soft brush made of special fiber that does not even scratch gold-plated surfaces
6V-shaped twin cyclones
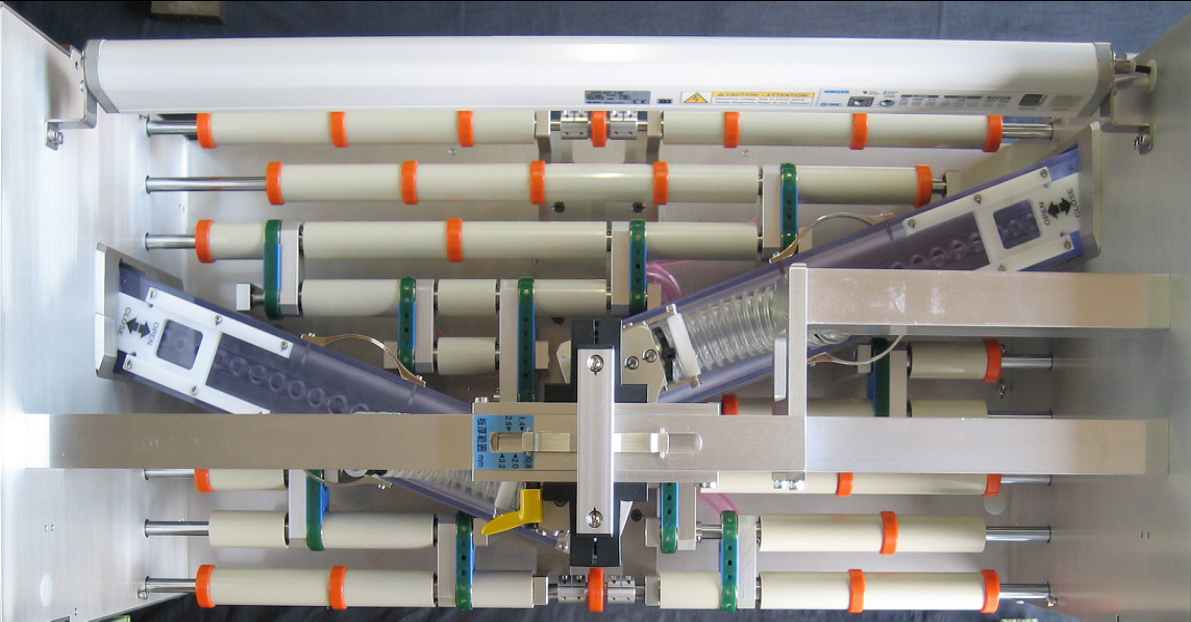
- Configuring cyclone heads in a V shape enables stable transport even with thin boards
- Standard with gap adjuster for top and bottom brushes for board thickness of 0.04-3.2mm
7Cyclone head
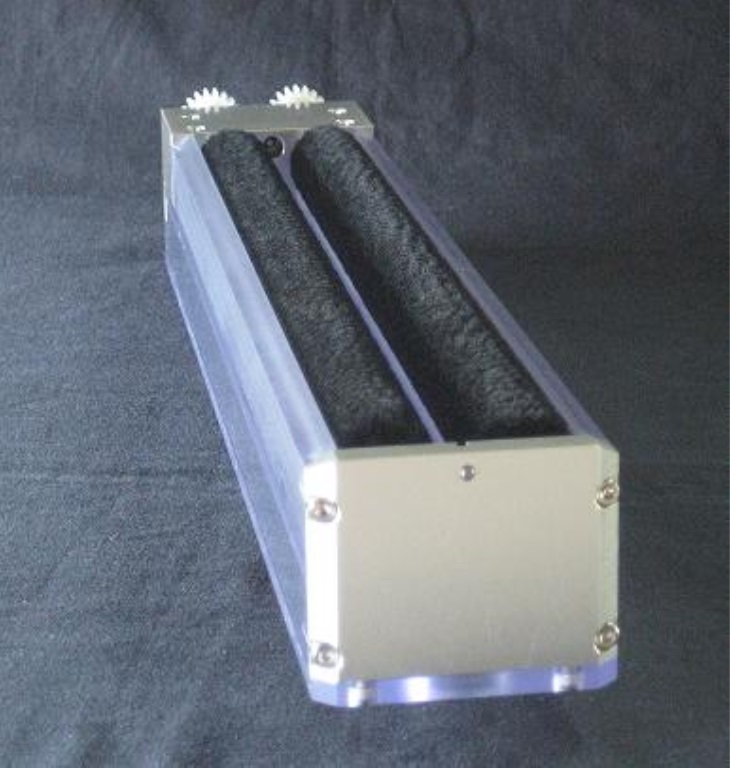
- User-friendly design enables very easy brush replacement
- Can be ordered in single units
※Manufacturer option
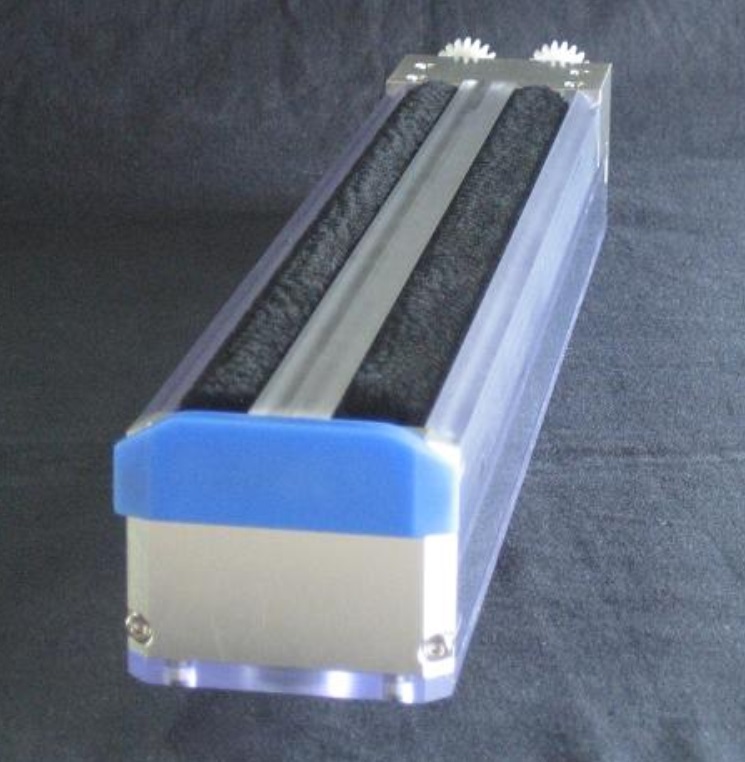
- Parts to enable processing of thin, fragile boards
※Manufacturer option
- Reduced entrainment in brush
- One-touch desorption
8Adsorption conveyor
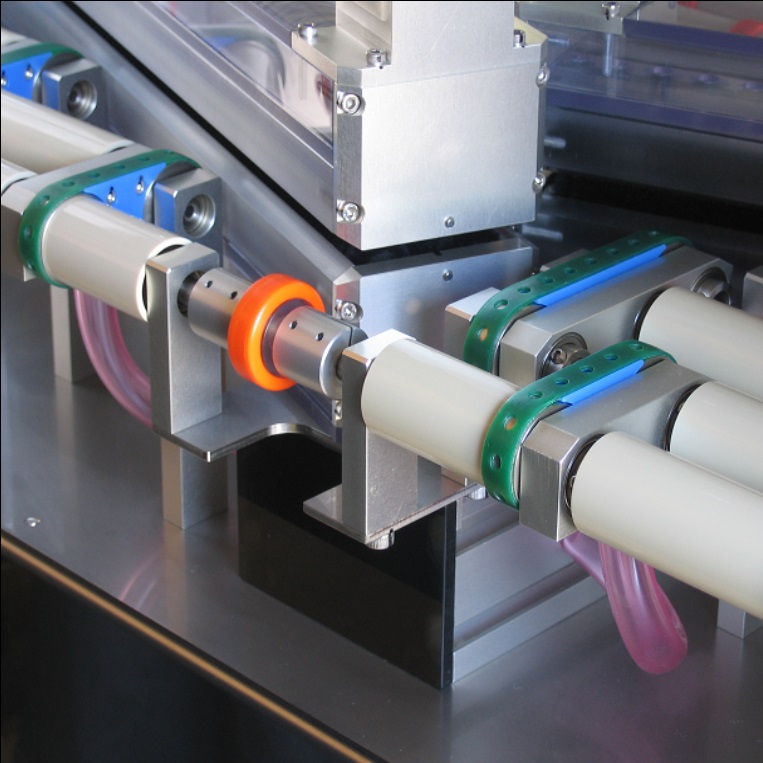
- Original adsorption belt and transport conveyor of polyurethane
- Max. belt and roller electrostatic voltage of 50V
9Unit for supporting warped board
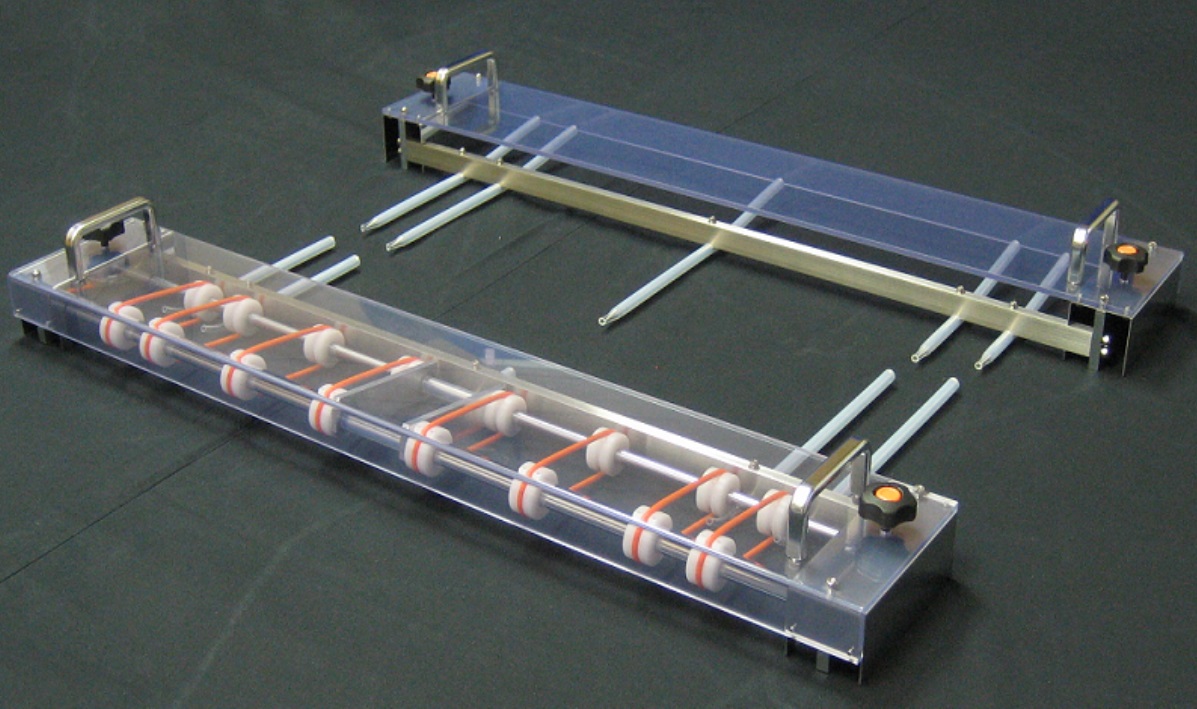
※Manufacturer option
- Unit that supports boards with warpage up to 10 mm
- Uses introduction drive belt method
10Clear window
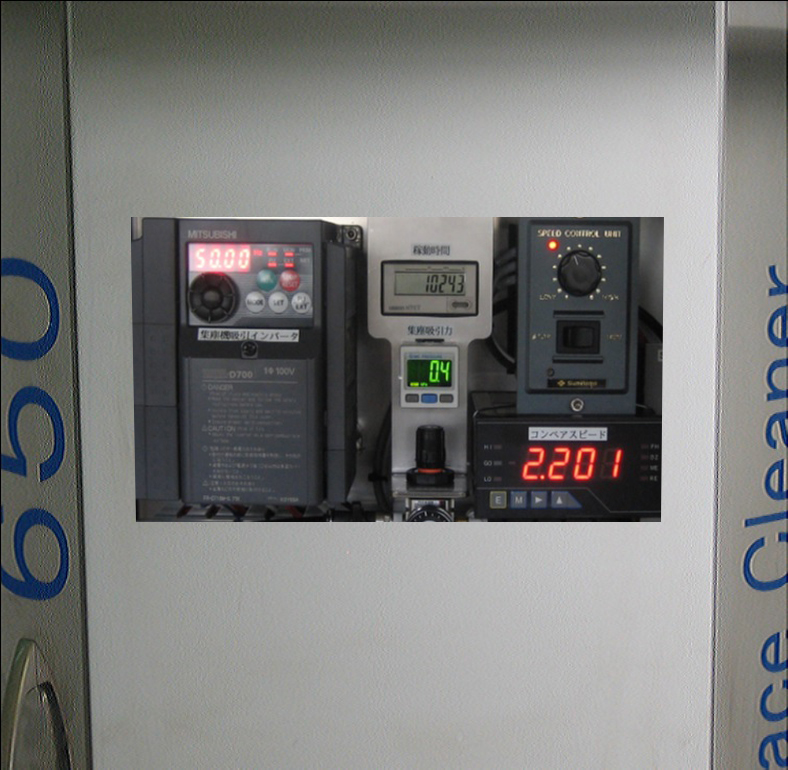
Enables operational state of system (e.g., inverter that controls dust collector, conveyor speed) visible from the outside
11
※ Manufacturer option
Charge/discharge conveyor
L900, L615, L325 are available (L615 is fitted in photo)00~1100mmまで対応
12
※Manufacturer option
Pass line change
Support for 900-1,100mm
Features
Equivalent capacity to 5 adhesive rollers in series
Contaminant removal capacity with adhesive rollers on flat surfaces is complemented by the brush follow-up in the grooves after pattern circuit formation.
It is particular good in terms of production run rate in AOI processes (reduction in false reports)
Reduced running cost
The only consumable parts are the 8 brushes, helping to reduce your costs.
(Brush replacement yardstick: 600-1,800h)
Effective for a variety of processes
Here are some examples of effective application of brush-type cyclone cleaners (VSC).
Process |
Example of effective application |
Before dryfilm pasting |
Removes 96% or more of the dust that tends to degrade exposure. |
Before exposure |
Removes 96% or more of the dust that tends to degrade exposure. |
Before AOI |
Sharp drop in false reports with AOI, and synergistic effect up to stage between AOI and verification, with no stagnation boards. |
Before roughening |
Sulfuric acid tank maintenance is needed at least 3 times less frequently. |
After V-cutting/
Routing/drilling holes |
With clean rollers, adhesive film quickly became contaminated with cutting waste, and cleaning could not keep up. Switched to VSC for this reason. |
Laminating paper cleaning |
Switched to VSC from water cleaning because it is equally effective. Cleaning is now possible any time. 98% or more of copper particles stuck on the paper surface are removed. |
After laser making, before water cleaning |
The phosphorus level in the water cleaning tank dropped sharply, so tank maintenance is needed at least 5 times less often. |
Throughout pattern formation |
Up to L/S75µm The dust from crevices, which are difficult to clean using clean rollers, can be cleaned out effectively with VSC. |